A new Lean Moving Line for thrust reverser production
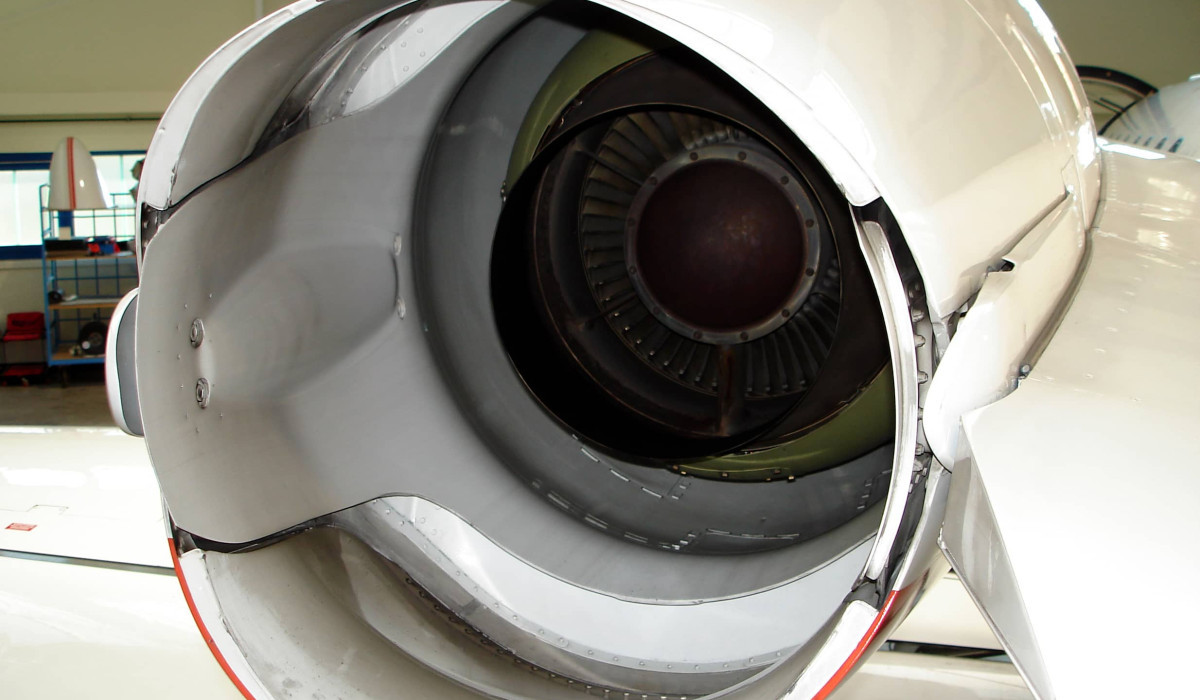
-
SectorAeronautics
-
Size of entitySite of 450 people
-
Challenges of the missionThe main challenge for us was the interweaving of the various parties, both customers and subcontractors, who had to install the infrastructure: frames, handling, robotics, automation specialists, etc., all of which were involved in the project.
Client context
This project was designed to meet the needs of the plant on its thrust reverser line for its major customer. It wanted to improve its performance in terms of productivity (hours spent per reverser), investment (number of workstations) and lead time.
The challenge is to take advantage of the levelling effect of production volumes in 2017 to prepare comfortably for the ramp-up in 2018 (15 aircraft per month is considered the peak).
Support put into place
We worked iteratively on this project, as we had to quickly establish an industrial vision, estimate the requirements for the moving line (number of stations and racks, length of line, etc.), and then work out and dimension each station in detail.
This involves drawing up standards with the operators, managing station supplies and integrating the work of the controllers into the balancing of the line. Together with the project team, we have structured the management of the MBOM update, taking into account the developments arising from the design office. The physical implementation of the new organization was supported by the start-up of the moving line: the frames move forward at around 1m per hour.
This mechanical advance helps to create a results-oriented culture with the field teams, as we can emulate a team on a very concrete physical event: the product leaves the work area at the end of Takt Time.
We've worked hard with front-line management to support them in their new environment, notably through specific training sessions for which we created a model of the plant. This model and some of the training courses were integrated into the integration program for plant managers.
Finally, one last subject, typical of Lean Manufacturing in the Industry sector, was addressed as part of the project: logistics. We worked on making the right parts available to the workers on the line, and creating a supermarket to carry out picking operations to supply the line. And we worked with the supply team to ensure that even the tightest supplies were available, so as to limit chain breaks.
-
Length of the mission13 months
-
GEOLEAN Team (FTE)4
-
P&L earningsPer year: €2.6M at a rate of 15 aircraft/month
Reduction in investment required: €1.2M
Results
- Productivity: 45% reduction in hours spent per inverter
- Capacity: from 6 to 10 inverters per week
- Reduction in number of stations: from 17 to 12