How a glass manufacturing plant in Poland became a performance benchmark for its group
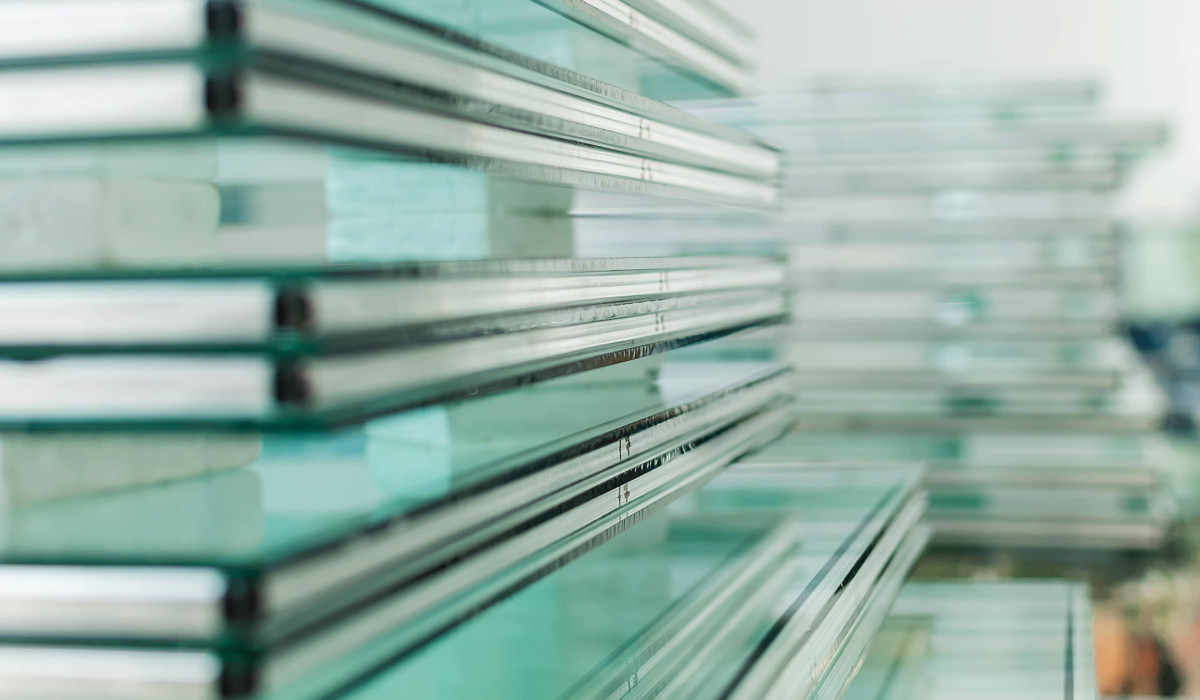
-
SectorGlass industry
-
Size of entitySite of 110 pax
-
Challenges of the missionGetting people to want to look at work differently, when the plant has been operating smoothly for over 20 years.
Client context
Our customer is a manufacturer of glass for the building industry. In addition to productivity, the cost of materials is an important issue, as it represents the plant's biggest expense. The challenge was to find an organization that would optimize raw materials and ensure a short lead time and an on-time delivery rate of over 95%. We cut glass, process it (tempering, silk-screening, polishing) and manufacture double glazing, in sizes ranging from a few dozen cm2 to several m2.
Performance has improved to such an extent that this plant has become a benchmark within the European group.
Support put into place
We tackled several Lean Manufacturing levers in order to achieve the expected results: working on synchronization between the different processes in order to free up capacity reserves (the downstream process no longer waits for the upstream process). Sorting logic and the associated visuals to facilitate it were key to success, as operators no longer lost time. And above above all, the layout of the lines facilitated sorting maneuvers, reducing breakage by almost 40%.
This enabled us to free up surface area and thus increase the optimization window for cutting, which in turn generated a gain in off-cuts. We have translated this change into the way we plan production runs.
The last major productivity / capacity lever on the double glazing lines was to focus the production team on a concrete objective: the press never stops. This translates into “the press is always fed” and also “the end of the line must always be evacuated”. This organization, co-constructed with the teams in the field, holds up because the production manager was the project leader and was able to question his way of seeing production and then pass it on to his teams.
-
Length of the mission11 months
-
GEOLEAN Team (FTE)A team of 3 persons to support the customer's teams
-
P&L earnings750 K€ annually
Results
- Productivity/capacity: 25%.
- Yield: 15% material scrap reduction
- OTD: 96