Capacity
Productivity
Safety
How to speed up production and make it more efficient
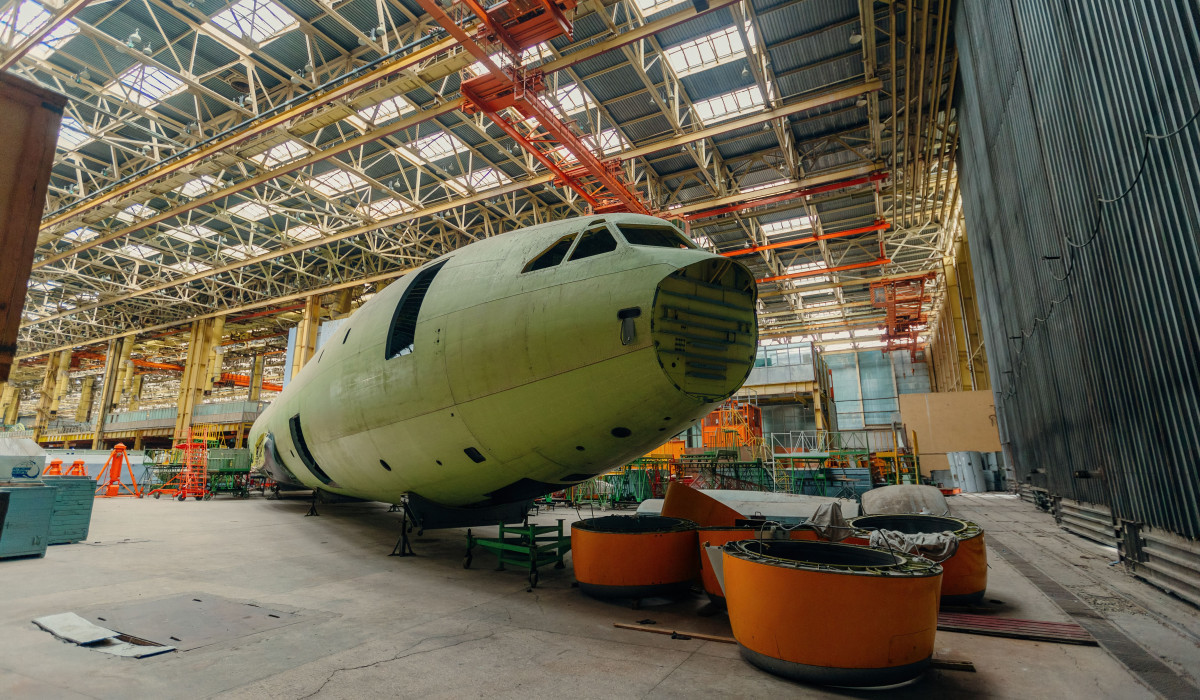
-
SectorAeronautics
-
Size of entitySite with 500+ people, 150-person perimeter
-
Challenges of the missionGet everyone involved to work together: production, logistics, design, technical preparation, etc.
Client context
The need was to reduce the Production Interval (PI) from 19 days to 10 days, in a context of increasing customer demand with new export sales.
Initial findings revealed the following loss-making factors:
- Time wasted in finding the right parts (delivery of large crates of different parts to the edge of the line).
- Journeymen would go to the logistics store themselves to replenish their supplies of hardware and cutting tools, or when a part was missing.
- Workers changed shifts and products in progress remained stationary, as production was organized in Docks.
- Ergonomics/safety: risk of falling, high-rise workstations not secured.
Support put into place
- Line up the workshop. This was done in conjunction with the journeymen: we took all the instruction sheets that had been annotated by the journeymen for years, and created a product sheet. This enabled us to build a line balancing system together, and to determine the tools, parts and resources required for each workstation.
- Creation of new frames to improve work ergonomics and ensure safety (working on the ground as much as possible, and installation of a secure footbridge when working at height).
- Implementation of Lean logistics: supermarket and small train: 2x delivery per shift to bring the necessary parts kits to the line edge: control of the backlog.
- Introduction of a new human resources organization: performance and contingency management, introduction of reference journeymen, integration of control into the UAP, etc.
-
Length of the mission20 months
-
GEOLEAN Team (FTE)4 persons
-
P&L earnings2,2 M€ annually
Results
- Capacity: installation of a line taking out a complete section and checked every 10 days
- Productivity: 46% reduction in hours clocked per section
- WIP: reduction from 9 (at PI 19) to 6 (at PI 10), i.e. 52%.
- Cycle time: reduction from 179 days to 82 days, i.e. a 52% reduction
What our clients say
Want to know more?
Contact